Performance Improvement through Implementation of Lean Maintenance
DOI:
https://doi.org/10.26703/jct.v6i2.341Keywords:
TPM, Total Productive Maintenance, Predictive Maintenance, RCMAbstract
Lean Maintenance is a relatively new term, invented in the last decade of the twentieth century, but the principles are well established in Total Productive Maintenance (TPM). Lean Maintenance—taking its lead from Lean Manufacturing—applies some new techniques to TPM concepts to render a more structured implementation path. Tracing its roots back to Henry Ford with modern refinements born in Japanese manufacturing, specifically the Toyota Production System (TPS). Lean seeks to eliminate all forms of waste in the manufacturing process—including waste in the maintenance operation. Plants can accelerate their improvements with much lower risk through the elimination of the defects that create work and impede production efficiency. Optimizing the maintenance function first will both increase maintenance time available to do further improvements and will reduce the defects that cause production downtime. Thus cost reduction and improved production are immediate results from establishing Lean maintenance operations as the first step in the overall Lean Enterprise transformation. This paper discusses the application of lean principles in maintenance of aircraft, and describes some of the lean tools and techniques that are being used to transform maintenance process. This research study was based upon defects occurred on ten aircrafts for the period of three years in one of the private aviation industry. System wise defects data were collected and the effect of the trend of these effects was investigated thoroughly.
Downloads
References
Womack J.P and D.T. ‘Lean Thinking’, Simon and Schuster (1996)
T.Ohno, Toyota production system, Beyond large scale production, productivity press 1988 pp.25-29
“Lean Maintenance” - Reduce cost, improve quality and increase market share by Ricky Smith and Bruce Hawkins
M. Poppendieck, Principles of LEAN thinking, Onward-17th Annual ACM Conference on Object-Oriented Programming, Sys. Languages and Applications, Washington 2002.
A. Smalley, Lean and the Law of Unintended Consequences, Super factory www.lean.org. (2005)
Womack J.P, Jones DT, Roos D (1990) The machine that changed the world, Machmillan, New York.
Lee-Mortimer A (2006) A Lean route to manufacturing survival, Assem Autom 26(4); 265-272
Holweg M (2007). The genealogy of lean production. J.Oper Manag 25(2);420-437 doi;10,1016/j.jom.2006.04.001
Morgan J and J.K. Liker. ‘The Toyota product Development system: Integrating people, process and Technology, New York. Productivity press 2006.
Rother. M and Shook J: Learning to see: Value stream mapping to add value and Eliminate MUDA Brookline: Lean enterprise Institute, 1999.
Schuh, G: Lean Innovation- Die Handlungsanleitung in 4th Lean management summit- Aachener management Tage, G Schuh and B Wiegend, Ed, Aahen: Apprimus-Verlag,2007
Adams E.K. and Willetts K.J. ‘The lean communication provider McGraw-Hill (1996)
Wilson P, Dell.L and Anderson G ‘ Root cause analysis - a tool for total quality management.’ ASQC Quality press 1993.
Mayhew A J and Stockton DJ ‘Cost-reduced cable delivery for the 21st century’, B.T Technol J, 16, No.4 PP22-100 (1998).
Krause.D & Temple V 1998, Maintenance management In: ‘Water system operation and maintenance workshop, Session notes, Denver, Co.
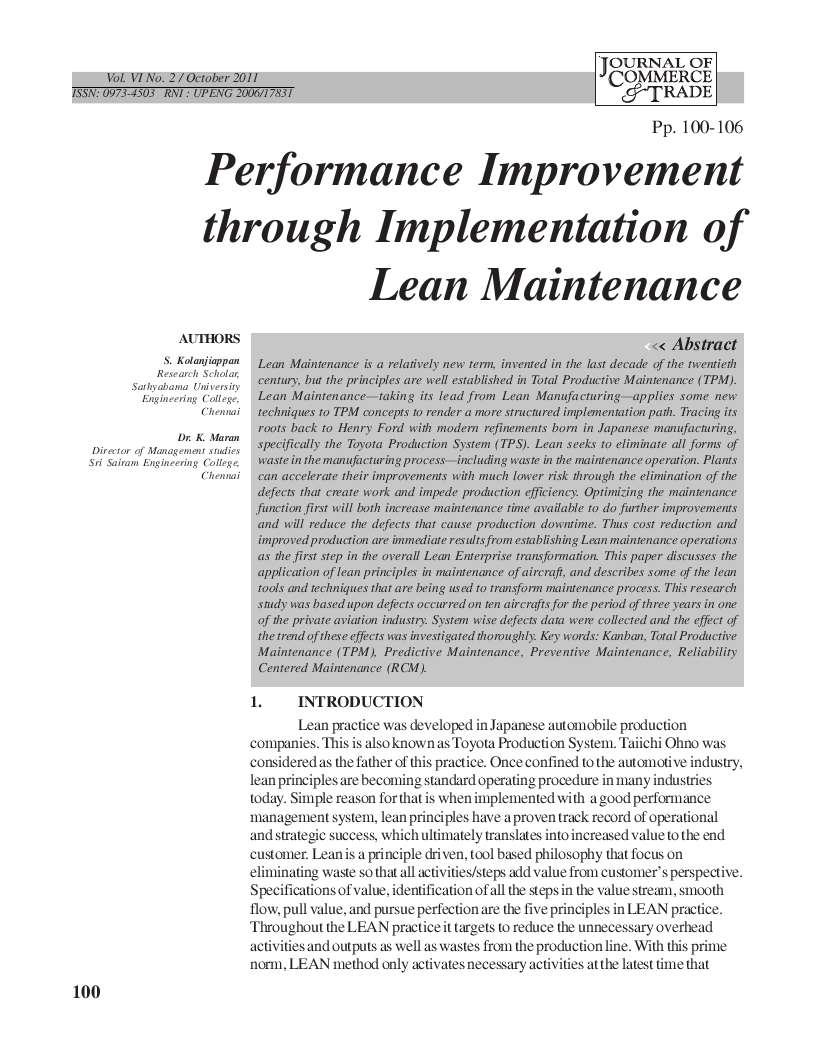
Downloads
Published
Issue
Section
License
Copyright (c) 2011 S. Kolanjiappan, Dr. K. Maran

This work is licensed under a Creative Commons Attribution 4.0 International License.